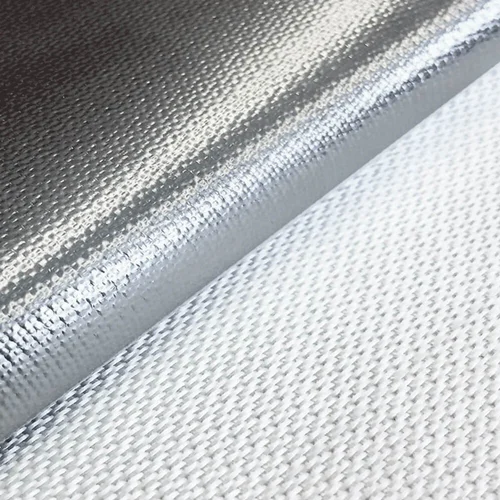
Introduce
Introduction to glass fiber and composite materials
Glass fiber (abbreviated as glass fiber) is a fibrous material drawn from molten glass. Due to its excellent mechanical strength, good insulation performance, corrosion resistance and light weight, glass fiber has become one of the indispensable important materials in industrial production and daily life. Glass fiber composite materials are a high-performance composite material formed by combining glass fiber as a reinforcing material with a matrix material (usually a polymer resin) through certain process means. This composite material not only inherits the advantages of glass fiber, but also can adjust its performance according to different application requirements, making it widely used in many fields.
Research background and significance
With the acceleration of global industrialization, the requirements for materials are also increasing. Although traditional metal materials perform well in many aspects, they are incapable of doing so in some application scenarios due to their heavy weight and easy corrosion. Glass fiber and its composite materials have attracted much attention due to their unique performance advantages. Especially in the construction, automobile, aerospace and other industries, glass fiber composite materials have become an ideal choice to replace traditional materials due to their lightweight and high strength.
In addition, with the improvement of environmental protection awareness, people pay more and more attention to the environmental protection properties of materials. Glass fiber composites have great potential in the field of green building materials due to their good recyclability and low energy consumption. Therefore, in-depth research on glass fiber and its composite materials will not only help promote technological progress in related industries, but also promote sustainable economic and environmental development.
At present, research on glass fiber and its composite materials has achieved remarkable results. New materials and new processes continue to emerge, such as carbon nanotube reinforced glass fiber composites, graphene reinforced composites, etc., which have greatly expanded the application range of glass fiber composite materials. At the same time, there have been great progress in preparation technology, such as the use of 3D printing technology to directly manufacture complex glass fiber composite structural parts, which has improved production efficiency and reduced costs.
However, in the face of growing demand, glass fiber and its composite materials still face some challenges. How to further improve the performance of materials, reduce production costs, and achieve large-scale commercial applications are all key research directions. In the future, with the advancement of science and technology and changes in social needs, the research on glass fiber and its composite materials will continue to develop in the direction of high performance, multifunctionality and intelligence. It is expected that in the near future, glass fiber composite materials will play an important role in more fields and become one of the important forces to promote scientific and technological progress.
Basic properties of glass fiber
Definition and classification
Glass fiber is a kind of slender fiber made from molten glass by a special process. It is usually made of silicon dioxide (SiO₂) as the main component, plus a small amount of aluminum oxide (Al₂O₃), calcium oxide (CaO), magnesium oxide (MgO) and other auxiliary components. According to different formulas and production processes, glass fiber can be divided into many types, the common ones are:
E glass fiber (Electrical): This is the most commonly used type of glass fiber, with good electrical insulation and mechanical strength. E glass fiber is mainly composed of silicon dioxide, aluminum oxide, calcium oxide and other trace elements.
C glass fiber (Chemical): This type of glass fiber has strong acid and alkali corrosion resistance and is suitable for anti-corrosion materials in the chemical industry.
S glass fiber (Strength): This type of glass fiber has excellent mechanical properties and is mainly used in occasions with high strength requirements, such as aircraft parts, advanced composite materials, etc.
A glass fiber (Alkali): Contains a higher amount of alkali metal oxides and is suitable for certain specific industrial uses.
AR fiberglass (Anti-corrosion and Alkali-resistance): This type of glass fiber is both alkali-resistant and corrosion-resistant and is often used as a reinforcing material in the construction industry.
Physicochemical properties
As an amorphous solid material, glass fiber has a series of excellent physical and chemical properties, which make it widely used in many fields:
Mechanical properties:
High strength: Glass fiber has high tensile strength and can withstand large external forces without breaking.
High modulus: Compared with ordinary metals, glass fiber has a higher elastic modulus, which means that it can maintain good rigidity under stress.
Heat resistance and corrosion resistance:
High temperature resistance: Most glass fibers can be used for a long time in an environment up to several hundred degrees Celsius without significant changes.
Corrosion resistance: Glass fiber is not easily corroded by water, oil or other corrosive media, which makes it used in chemical equipment, pipelines and other fields.
Optical properties:
Transparency: Some types of glass fiber can be used to make optical fibers for data transmission.
Reflectivity: Glass fiber has a smooth surface and high reflectivity, and can be used to make reflective materials.
Electrical properties:
Insulation: Glass fiber has good insulation properties and is often used to make insulating materials.
Dielectric constant: Its dielectric constant is low and it is suitable for the insulating layer in high-frequency electronic equipment.
Other characteristics:
Density: The density of glass fiber is relatively small, about 2.5 g/cm³, which is much lighter than steel.
Hygroscopicity: Glass fiber itself has weak hygroscopicity, but it may absorb moisture in a humid environment, affecting its performance.
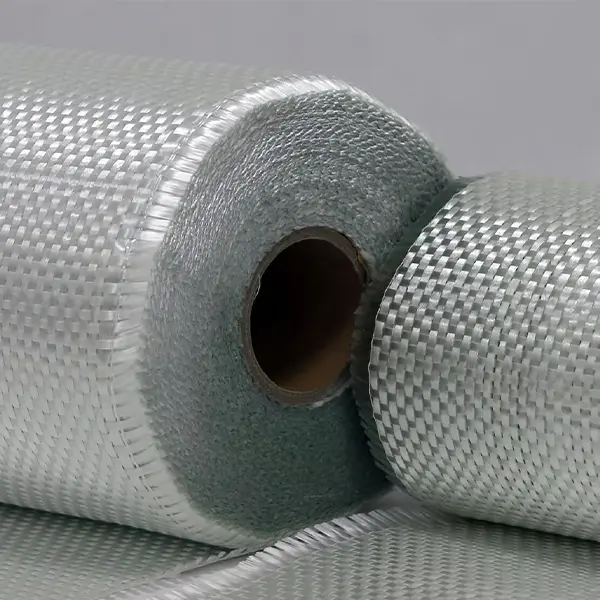
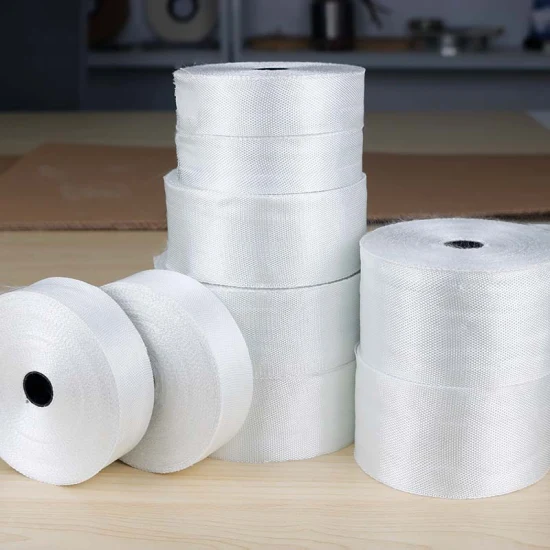
Manufacturing process
The production of glass fiber mainly relies on two methods: wire drawing and injection molding.
Wire drawing:
Direct wire drawing: The molten glass liquid is passed through a metal plate with many small holes, and a high-speed rotating wire drawing machine is used to draw out thin and long fibers.
Indirect wire drawing: The molten glass liquid is first made into a preform, and then it is drawn into fibers through a wire drawing machine.
Injection molding:
This method is suitable for the production of chopped fibers or fiber mats. The molten glass liquid is sprayed into fine fibers by high-pressure gas or steam, and then collected.
Application fields of glass fiber composite materials
Glass fiber reinforced plastics (GFRP) plays an extremely important role in modern industry with its excellent performance and diverse applications. The wide application of GFRP not only promotes the technological progress of related industries, but also drives the development of materials science. The following are typical applications of GFRP in construction, automobile manufacturing, aerospace and other high-tech industries.
Applications in the construction industry
Thermal insulation and sound insulation materials
GFRP has been widely used in building insulation materials due to its good thermal insulation and sound insulation effects. It can be made into panels or foam forms and used as insulation layers for walls and roofs to effectively reduce energy loss.
In terms of sound insulation, GFRP materials also perform well and are used to make facilities such as sound barriers and partition walls to help reduce urban noise pollution.
Structural reinforcement materials
In the process of renovation and reinforcement of old buildings, GFRP, as a lightweight and high-strength material, can be used to enhance the bearing capacity of structures such as beams, columns, bridges, and extend the service life of buildings.
At the same time, GFRP can also be used to make various building components, such as door and window frames, decorative panels, etc., which are not only beautiful, but also have good weather resistance and corrosion resistance.
Waterproof materials
In waterproofing projects, GFRP composite materials can provide reliable waterproofing solutions to prevent water leakage from damaging buildings.
Other applications
Such as swimming pool linings, trench covers, etc., the corrosion resistance and easy cleaning characteristics of GFRP materials make them ideal for these applications.
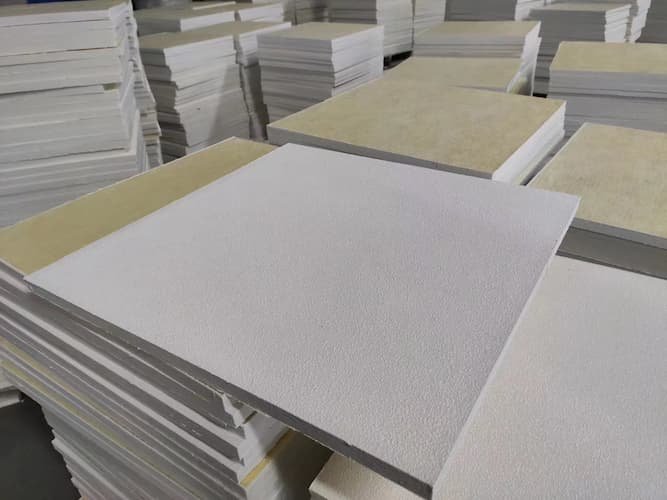
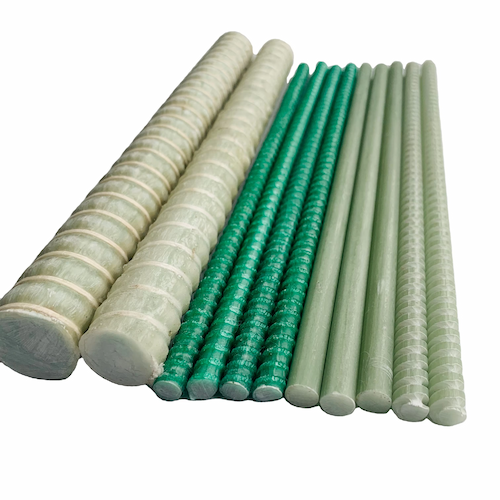
Application in the automotive industry
Weight reduction design
In the automotive industry, GFRP is widely used in the design and manufacture of body panels, interior parts and other parts due to its light weight and high strength, thereby reducing the overall weight of the vehicle, improving fuel efficiency and reducing emissions.
In addition to body parts, GFRP can also be used in engine hoods, fenders and other parts to further achieve the lightweight goal of the entire vehicle.
Wear-resistant parts
Inside the car, GFRP can also be used to manufacture wear-resistant parts, such as brake pads, drive shaft sleeves, etc., to extend the service life of the parts.
Enhanced safety
GFRP materials can be used to manufacture parts of collision buffers, increase the safety performance of the vehicle, and protect the safety of passengers.
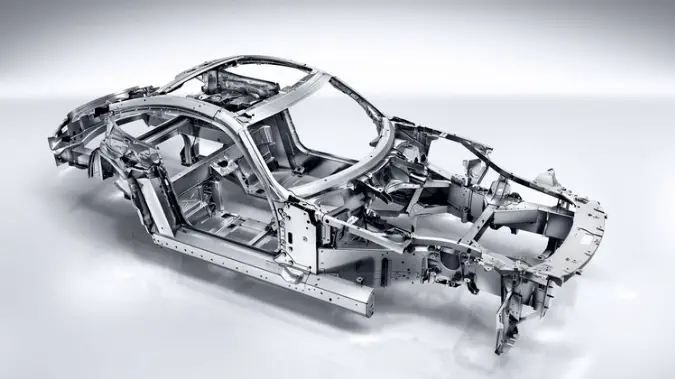
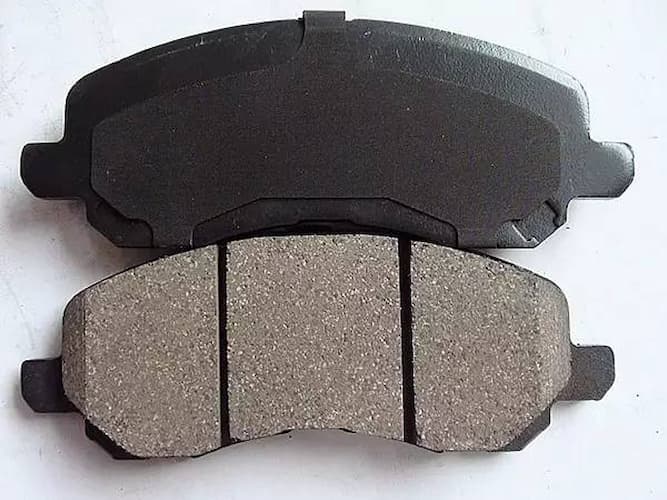
Applications in aerospace and other high-tech industries
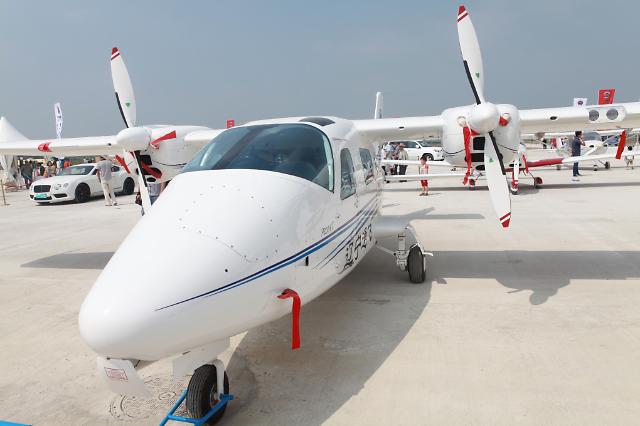
Application of composite materials in aircraft
In the aviation field, GFRP is widely used in key parts such as aircraft wings, fuselages, and tails due to its excellent mechanical properties and lightweight advantages, which not only reduces the weight of the aircraft, but also enhances the stability of the structure.
In addition, GFRP can also be used to manufacture aircraft interior materials, such as seats and luggage racks, to further reduce the load and improve flight efficiency.
The role of new energy technology
In the field of wind power generation, GFRP is used to make wind turbine blades, which not only need to withstand the centrifugal force generated by high-speed rotation, but also need to resist wear and damage under severe weather conditions.
GFRP is also used in the bracket system of solar photovoltaic panels to ensure the stability and reliability of photovoltaic panels.
Other high-tech industries
In the shipbuilding industry, GFRP is used to build hulls, decks and other components, improving the durability and navigation efficiency of ships.
In the electronics and electrical industry, GFRP is used to manufacture the shells of various electronic products, such as mobile phone back covers, laptop shells, etc., which are both beautiful and practical.
In the field of medical devices, GFRP is used to manufacture the support structure of operating tables and CT scanners due to its non-magnetic and good X-ray transmittance.
Research progress of glass fiber composite materials
With the continuous advancement of materials science and engineering technology, the research on glass fiber composites (GFRP) is also deepening, and new reinforcement materials, resin systems and manufacturing technologies are constantly emerging, which greatly enriches the application scenarios and performance of GFRP. The following are the main advances in the current research on glass fiber composites.
Carbon nanotube (CNTs) reinforcement
As a new type of nanomaterial, carbon nanotubes have extremely high specific strength and specific modulus. Adding CNTs to GFRP can not only significantly improve the mechanical properties of the composite material, but also improve its electrical and thermal conductivity.
Research shows that by dispersing CNTs evenly in the matrix through appropriate methods, agglomeration can be effectively avoided and the overall performance of composite materials can be further optimized.
Graphene enhanced
Graphene is a two-dimensional material with a single atomic layer thickness and excellent mechanical strength and electrical conductivity properties. Introducing it into GFRP can greatly improve the mechanical properties of the material while giving it electromagnetic shielding and other functions.
Due to the size effect of graphene, how to achieve uniform dispersion in composite materials has become one of the focuses of research.
Nanoscale fillers
In addition to CNTs and graphene, other nanoscale fillers such as nanosilica, nanoclay, etc. have also been widely studied for reinforcing GFRP. These fillers can improve the interface bonding force of composite materials and improve their toughness and impact resistance.
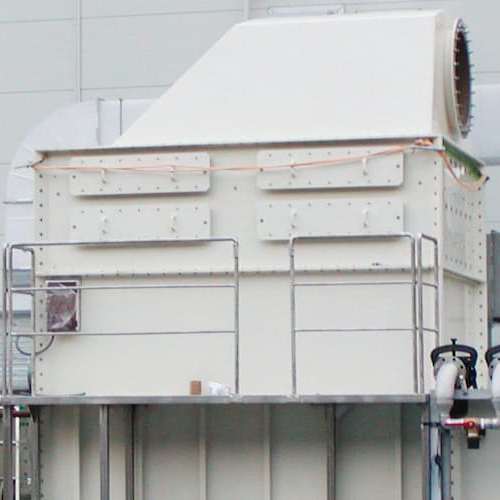
Biodegradable resins
With the improvement of environmental awareness, the development of biodegradable resins has become a research hotspot. This type of resin can not only decompose in the natural environment and reduce environmental pollution, but also its preparation process is more green and low-carbon.
At present, some resins based on natural polymers (such as starch, cellulose, etc.) have been successfully used in the preparation of GFRP.
High-temperature stable resins
In high-temperature working environments such as aerospace and automobile engines, traditional epoxy resins are difficult to meet the requirements of use. Therefore, the development of resins with higher thermal stability has become an inevitable trend.
Studies have shown that the heat resistance of materials can be effectively improved by introducing heat-resistant groups or using resin systems with higher cross-linking density.
Functional resins
In order to meet specific functional requirements, researchers have begun to explore resins with special functions, such as conductive resins, self-healing resins, etc. These resins can give additional functional properties to composite materials and broaden their application range.
3D printing technology
3D printing technology (additive manufacturing) has been widely used in the field of composite materials in recent years. By precisely controlling the material deposition process, GFRP parts with complex shapes can be manufactured, improving material utilization and shortening the production cycle.
Researchers are exploring the combination of different types of reinforcement materials with resins to prepare composite materials with excellent performance through 3D printing technology.
Microwave curing technology
Microwave curing technology uses the principle of microwave heating to accelerate the resin curing process, greatly reducing the curing time and energy consumption. This method is particularly suitable for large-scale continuous production of GFRP products.
Microwave curing technology can also improve the uniformity of composite materials, reduce defects, and further enhance material performance.
Automated laying technology
Automated laying technology (such as automatic fiber placement AFM and automatic tape placement ATL) can realize the automated laying of fiber prepregs, improve production efficiency, and reduce quality fluctuations caused by human factors.
This technology is particularly suitable for the manufacture of large composite components, such as aircraft wings and hulls.
In Conclusion
By combing through the current research progress, this article points out the latest achievements of glass fiber composites in new reinforcement materials, new resins and manufacturing technologies. Studies have shown that the introduction of new reinforcement materials such as carbon nanotubes (CNTs) and graphene has greatly improved the performance of composite materials; the development of functional resins such as biodegradable resins and high-temperature stable resins has opened up new areas for the application of composite materials; and the innovation of manufacturing technologies such as 3D printing technology and microwave curing technology has provided the possibility of improving production efficiency and reducing costs. In summary, glass fiber and its composite materials, as a high-performance and multifunctional material, have played an important role in many industries. With the advancement of science and technology and the continuous growth of market demand, the research on glass fiber composites will continue to advance to a deeper level, and its application scope will continue to expand, bringing more possibilities for the development of human society.
Aiswix, as a company focusing on the research and development and production of glass fiber products, is committed to providing high-quality and high-performance glass fiber products. The company has an experienced R&D team who are constantly exploring the application of new technologies and new materials, striving to maintain a leading position in the fierce market competition. Aiswix’s products cover various types from standard glass fiber to specialty fibers, which can meet the needs of different customers.