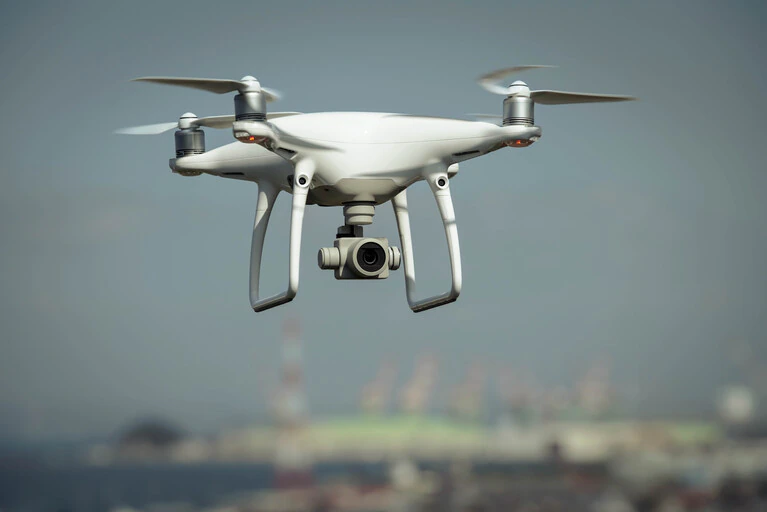
Introduce
With the rapid development of information technology, aerospace technology and new materials science, the UAV (Unmanned Aerial Vehicle) industry is growing at an unprecedented rate. From military reconnaissance to civilian logistics distribution, from film and television shooting to agricultural plant protection, the application scenarios of drones are becoming increasingly rich, and the market demand is showing an explosive growth trend. This phenomenon not only promotes the advancement of drone hardware technology, but also puts higher requirements on its manufacturing materials – light weight, high strength, high toughness, corrosion resistance and good processing performance have become the key indicators for the selection of drone materials.
Among the many available materials, glass fiber stands out due to its excellent physical and chemical properties and has become one of the focuses of drone manufacturers. Glass fiber is a fibrous material made of silica and other mineral components. It has very high tensile strength and low density. These characteristics make it very suitable for manufacturing various parts of drones. In addition, glass fiber also has good electrical insulation, heat resistance and anti-aging ability, and can adapt to various complex working environments, thereby ensuring the stable operation of drones under various conditions.
Since drones usually need to fly for a long time and over long distances, and in some cases need to carry a certain weight of payload, the weight control of the body is extremely strict. Glass fiber and its composite materials (such as glass fiber reinforced plastic, GFRP) can effectively reduce the weight of drones through their light and strong characteristics, thereby increasing their load capacity and range. In addition, in some tasks that require rapid response or high-speed flight, glass fiber materials can also help drones achieve higher maneuverability.
With the advancement of technology, researchers are constantly exploring new ways to improve the performance of glass fiber, such as enhancing its mechanical properties through nanotechnology, or mixing it with other high-performance fibers (such as carbon fiber) to achieve better overall performance. These efforts not only increase the design freedom of drones, but also provide manufacturers with more diversified material solutions. It can be foreseen that in the next few years, with the continuous advancement of materials science and the continuous innovation of drone technology, glass fiber will play a more important role in the field of drones, helping to create more efficient, reliable and versatile unmanned aerial vehicle systems.
Fiberglass Overview
Definition and classification
Glass fiber is a fibrous material drawn from natural minerals and synthetic materials after high-temperature melting. It is usually made of raw materials such as quartz sand, limestone, and borate through a series of complex processes. According to different uses and performance requirements, glass fiber can be subdivided into several types:
E-glass: This is the most common type, mainly used for electrical insulation and composite materials. E-glass has good electrical insulation, mechanical strength and chemical stability, and is suitable for making various composite materials and insulation products.
C-glass: This type of glass fiber is mainly used in acid and alkali resistant occasions because it has good resistance to acids and alkalis.
S-glass: Compared with E-glass, S-glass has higher mechanical strength and elastic modulus, and is suitable for applications with high requirements for tensile strength.
A-glass: Mainly used to reinforce plastic products, with good corrosion resistance.
AR-glass: This type of glass fiber contains flame retardants and is suitable for occasions that require fire resistance.
ECR-glass: Reinforced continuous fiber glass, mainly used in chemical corrosion protection, power and other fields, with good corrosion resistance and high mechanical strength.
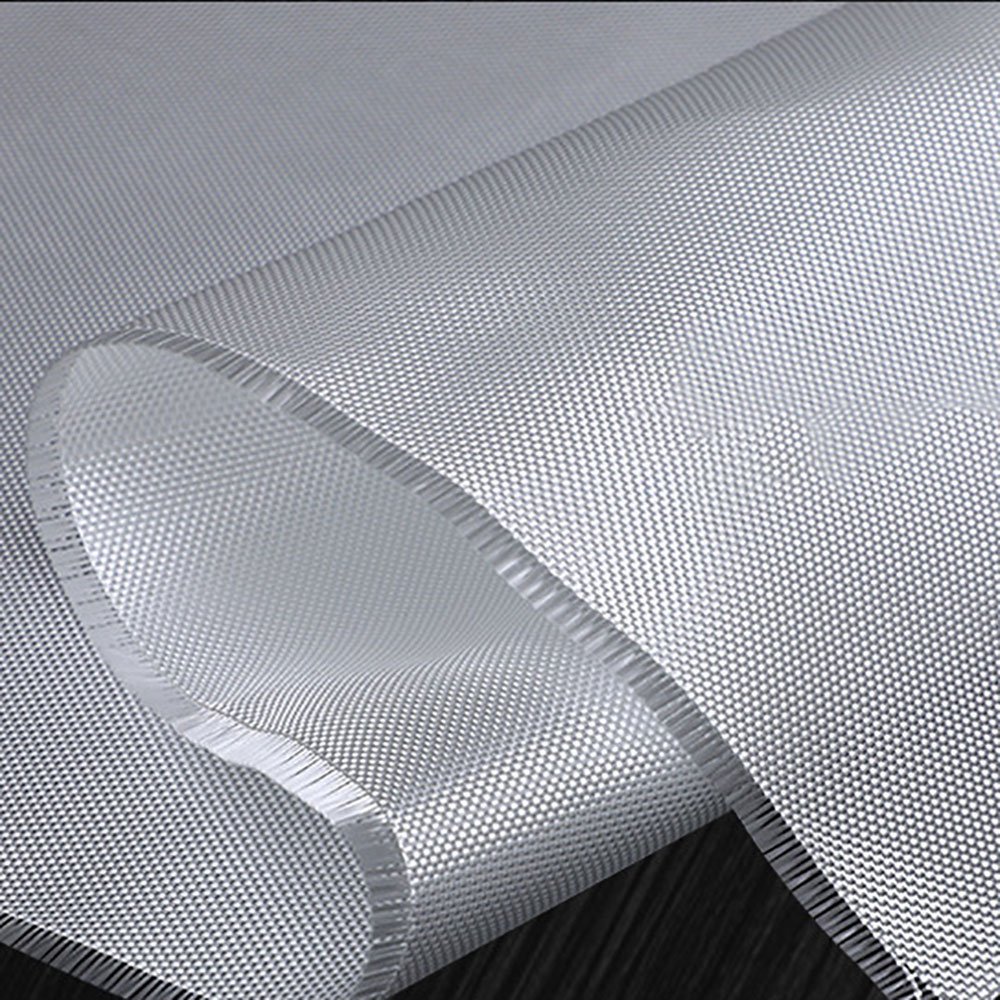

Manufacturing process
Raw material preparation: First, quartz sand, limestone, feldspar, magnesium oxide and other raw materials are mixed evenly in a certain proportion to ensure the quality consistency of the final product.
Melting: The mixed raw materials are sent to a high-temperature furnace and heated to above 1400℃ to completely melt the raw materials into liquid glass.
Wire drawing: The molten glass is drawn into filaments with a diameter of several microns to tens of microns through a specially designed nozzle. In this process, the diameter and strength of the fiber can be controlled by adjusting the temperature and tension.
Coating treatment: In order to improve the bonding performance between fibers, the fiber surface is often coated after wire drawing, and a coupling agent or other functional coating is added.
Curing: The coating is cured by heat treatment or other means to enhance the bonding force between fibers.
Finishing and packaging: Finally, according to different application requirements, the treated glass fiber is cut, woven, pressed into shape, and packaged and stored accordingly.
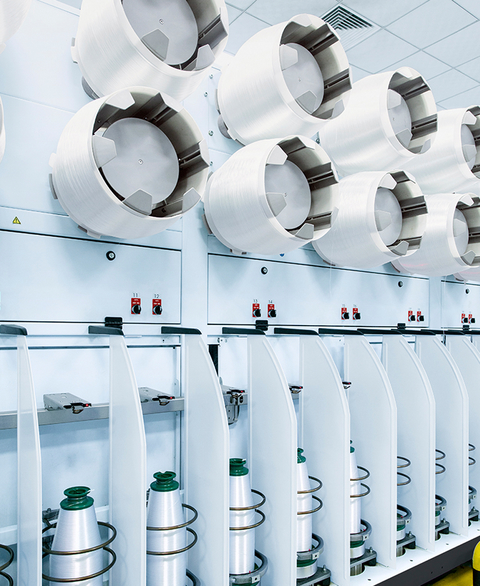
Performance characteristics
Lightweight and high strength: Compared with traditional metal materials, glass fiber has lower density and higher tensile strength, which is crucial for drones that pursue lightweight design.
Good mechanical properties: Glass fiber has high compressive strength, shear strength and fatigue resistance, and can withstand various mechanical stresses encountered by drones during flight.
Strong corrosion resistance: Glass fiber is not easily corroded by the atmosphere, seawater, oil and other chemicals, which makes it very suitable for drones working outdoors or in harsh environments.
Good electrical insulation: Glass fiber is almost non-conductive and has excellent electrical insulation properties, which is very important for protecting the safe operation of electronic equipment inside drones.
Processability: Glass fiber is easy to combine with other resins to form composite materials, and can be processed into the desired shape by injection molding, molding, etc., which greatly improves manufacturing flexibility.
Economic efficiency: Compared with some high-performance alloy materials, the price of glass fiber and its composite materials is relatively low, which is conducive to reducing the manufacturing cost of drones.
Analysis of UAV technology requirements
With the continuous development of drone technology, the market has higher and higher requirements for drone functions, especially in industrial applications such as logistics distribution, agricultural plant protection, environmental monitoring, etc. In order to meet these diverse needs, the design of drones must not only take into account structural optimization, but also functional expansion and technological development trends.
Structural
Lightweight: The weight of a drone directly affects its flight performance and endurance. In order to increase the load-bearing capacity of a drone and extend its flight time, the drone’s own weight must be reduced as much as possible. This requires the selection of lightweight materials, such as glass fiber composites, during design to achieve the best weight-to-strength ratio.
High strength: drones experience a variety of external forces during flight, such as wind, airflow, collision, etc. In order to ensure the safety and reliability of drones in complex environments, their structural materials need to have sufficient strength to resist the influence of these external forces.
Rigidity: When a drone is flying, especially at high speeds, the fuselage may deform. In order to avoid flight instability or control failure caused by deformation, the structural design needs to ensure sufficient rigidity to prevent deformation under stress.
Easy to maintain: drones will inevitably encounter damage or wear during use, so the detachability and replaceability of the structure should be considered during design to facilitate later maintenance work.
Modular design: With the diversification of drone application scenarios, modular design allows users to replace different functional modules according to actual needs, improving the flexibility and adaptability of drones.
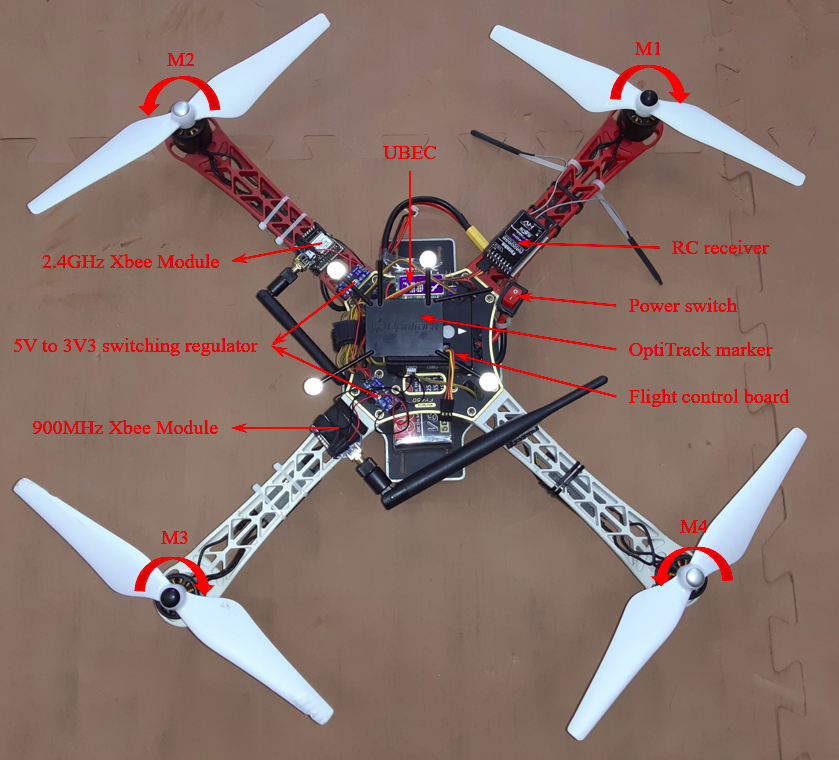
Functional
Logistics and distribution: In this scenario, drones need to have long endurance, large load space, and accurate positioning systems. In addition, they need to have good weather adaptability and be able to complete tasks under different climatic conditions.
Agricultural plant protection: Agricultural drones are mainly responsible for spraying pesticides and fertilizing. Therefore, they need to have accurate spraying control systems, stable flight platforms, and durable structures that can adapt to field operations.
Environmental monitoring: Drones used for environmental monitoring need to be equipped with various sensors, such as cameras, infrared imagers, etc., to facilitate data collection. At the same time, such drones also need to have a long flight distance and a high flight altitude to cover a wider area.
Film and television shooting: Drones used in the film and television industry are usually required to have stable flight characteristics and high-quality image transmission capabilities to ensure the clarity and smoothness of the captured images.
Emergency rescue: In emergency situations such as disaster relief, drones need to be able to be deployed quickly and have good communication capabilities and data transmission functions to facilitate real-time monitoring of the disaster and provide important information to rescuers.
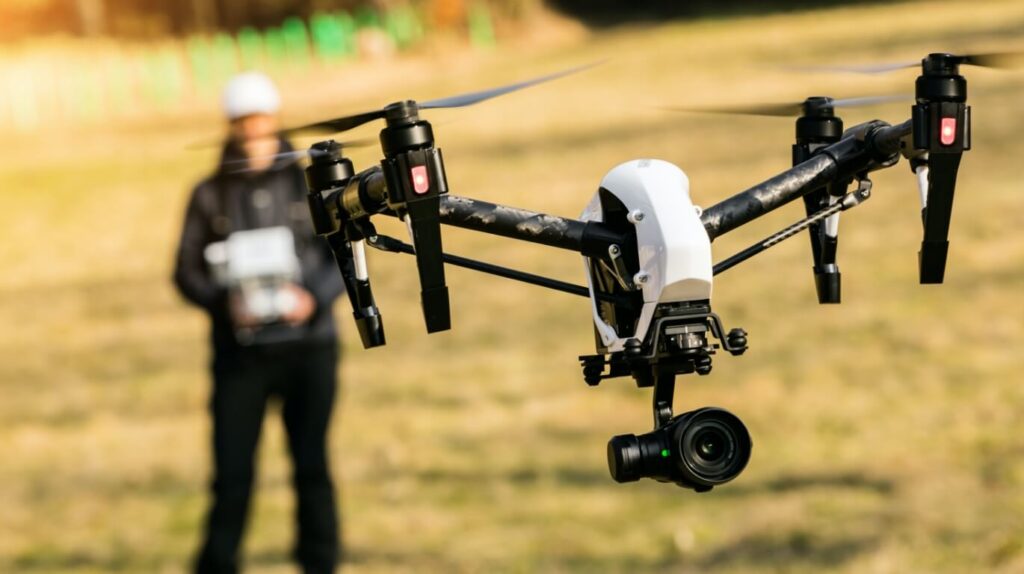
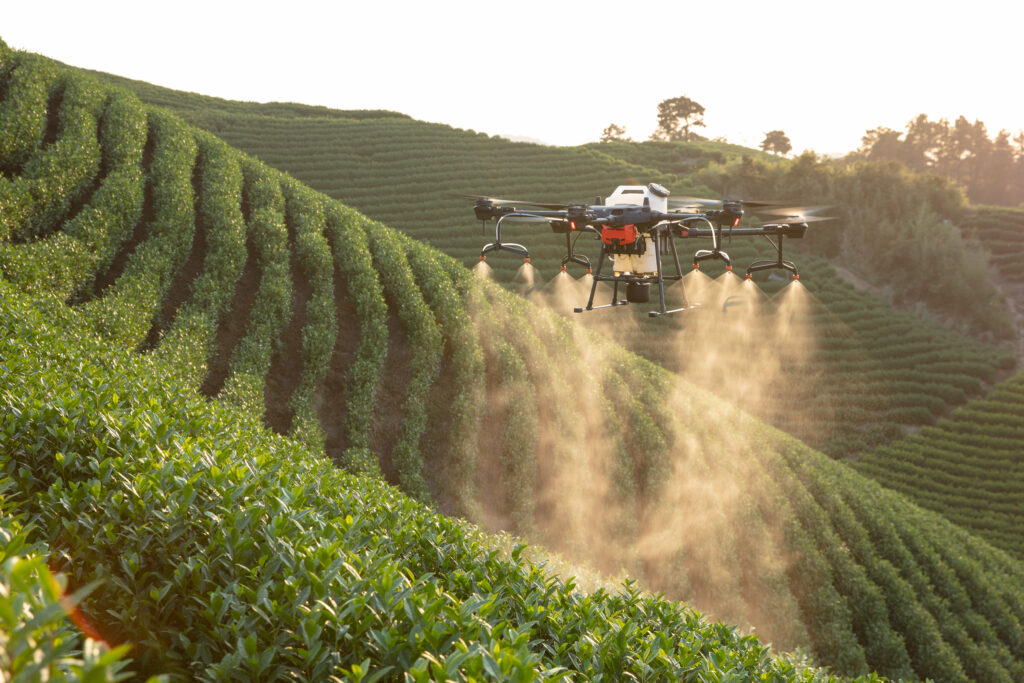
Technology
Intelligence: The application of artificial intelligence technology will enable drones to have stronger autonomous navigation and decision-making capabilities. By integrating machine learning algorithms, drones can better understand the surrounding environment and make more accurate action judgments.
Automation: With the development of automatic control technology, the operation of drones will become easier and easier, and even fully automated flight missions can be performed. Users only need to set the target parameters, and the drone can complete the task by itself.
Multi-machine collaboration: The future drone system will no longer be a simple operation of a single device, but a cluster of multiple drones working together. This will not only improve work efficiency, but also enhance the robustness of the system through distributed computing and resource sharing.
Energy innovation: With the development of new energy technologies, such as solar panels and hydrogen fuel cells, future drones are expected to achieve longer battery life and lower operating costs.
Material innovation: In addition to existing glass fiber composites, researchers are also exploring other new materials, such as carbon fiber and nanomaterials, to further improve the performance of drones.
Applications of glass fiber in drones
Wings and tail: Wings and tail are the main source of lift for a drone and an important part of flight control. Using glass fiber reinforced plastic (GFRP) as the material for the wings and tail can significantly reduce the weight of the drone while ensuring sufficient strength to resist aerodynamic loads during flight. In addition, GFRP also has good fatigue resistance and can withstand long-term flights without being prone to fatigue damage.
Fuselage Frame: The drone’s fuselage frame needs to support all the weight and maintain structural stability during flight. The fuselage frame made of fiberglass composite materials is not only light in weight, but also high in strength, which can effectively reduce vibration during flight and improve flight stability.
Landing gear: The landing gear of a drone is an important part to ensure a safe landing. Due to its good toughness and impact resistance, fiberglass composite materials are very suitable for manufacturing landing gear to cope with impact loads during landing.
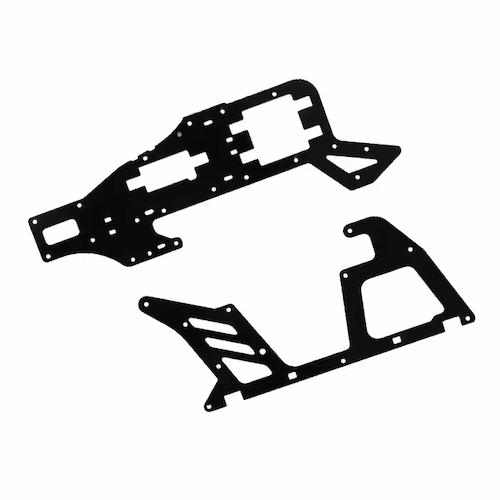
Rotor blades: The design of rotor blades needs to take into account weight, strength and aerodynamic efficiency. Rotor blades made of glass fiber reinforced plastic (GFRP) can maintain low weight while providing sufficient strength to withstand the centrifugal force generated by high-speed rotation. In addition, the smooth surface of GFRP helps to reduce air resistance and improve flight efficiency.
Rotor hub: The rotor hub is the component that connects the blades to the motor. Its strength and rigidity are essential to ensure the normal operation of the blades. The rotor hub made of glass fiber composite materials is not only light in weight, but also has high rigidity, which can effectively transmit torque and maintain the precise position of the blades.
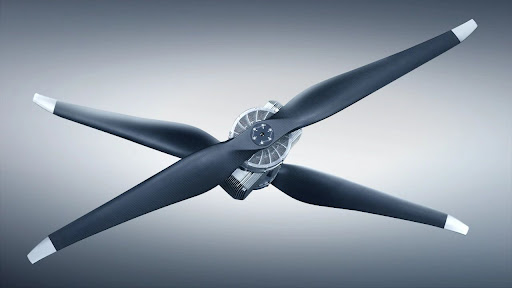
Body shell: The body shell of the drone usually needs to be dustproof, waterproof, and able to withstand certain external impacts. Using glass fiber reinforced plastic (GFRP) as the shell material can provide good protection while ensuring the lightweight of the fuselage.
Radome: The radome of the drone needs to have good electromagnetic wave penetration to ensure smooth signal transmission. Glass fiber composite materials are suitable for making radomes due to their good electrical insulation properties, which can protect the antenna from the external environment and will not interfere with signal transmission.
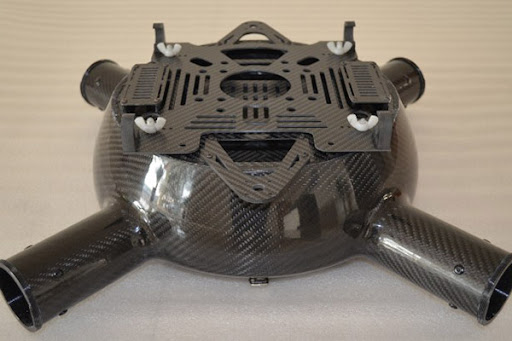
Battery compartment: The battery is the energy source of the drone, and the battery compartment needs to have good thermal insulation to protect the battery from overheating. Glass fiber composite materials can effectively reduce the impact of the external environment on the battery due to their good thermal insulation properties.
Camera bracket: The camera carried by the drone needs to be fixed in a specific position and remain stable. The camera bracket made of glass fiber composite materials can provide sufficient strength and stability to ensure the quality of the captured image.
Sensor protective cover: The various sensors installed on the drone also need proper protection. Glass fiber composite materials can be used to make sensor protective covers, which are both light and durable and can effectively prevent the sensor from being damaged.
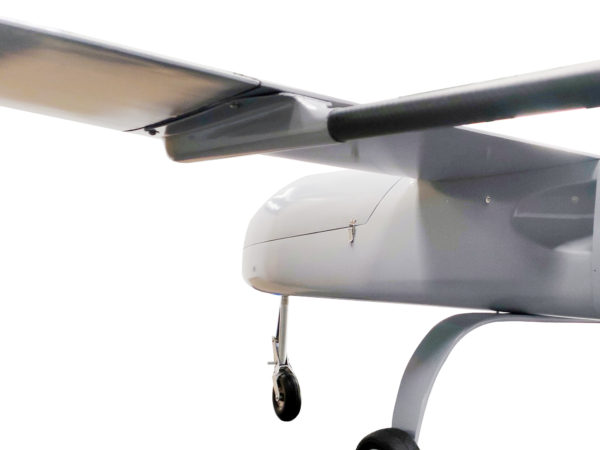
Optimizing UAV performance with fiberglass
As an advanced composite material, the application of glass fiber in UAV manufacturing is not limited to providing lightweight and high-strength structural support. More importantly, it can improve the overall performance of UAVs from multiple dimensions, including load capacity, flight time, cost-effectiveness and maintainability.
Load Capacity
Lightweight design: The density of glass fiber and its composite materials is much lower than that of traditional metal materials, which means that for the same volume of material, parts made of glass fiber are lighter. This allows the drone to significantly reduce its own weight while maintaining structural strength, leaving more weight space for increasing the payload.
Optimize structural layout: Using the plasticity of glass fiber, designers can flexibly design the structure of the drone according to specific needs, such as further improving the load-bearing capacity of the drone by strengthening key stress-bearing parts or optimizing the overall layout.
Enhance power system efficiency: Due to the lightweight characteristics of glass fiber materials, the power system of the drone does not need to output too much power to drive its flight, which indirectly improves the efficiency of the engine, allowing it to focus more on increasing the load rather than consuming it to offset the impact of additional weight.
Battery
Weight reduction: As mentioned earlier, using fiberglass can significantly reduce the weight of your drone. The reduced weight means less energy is required to fly, extending the drone’s endurance.
Improve energy efficiency: In addition to directly reducing energy consumption, lightweighting also reduces the resistance encountered by drones when flying in the air, thereby reducing the energy consumption required to maintain flight status. This also helps extend the flight time of the drone.
Enhanced power system efficiency: Since the power system does not need to overcome excessive weight burden, it can work more efficiently, further extending the drone’s endurance.
Cost-effectiveness
Reduce material costs: Compared with some high-performance alloy materials, the price of glass fiber and its composite materials is relatively affordable, which allows manufacturers to effectively control production costs while ensuring the performance of drones.
Reduce maintenance costs: Glass fiber has good corrosion resistance and aging resistance, which means that drone parts made of this material have a longer life and reduce the cost of frequent replacement due to material aging.
Improve operational efficiency: Because glass fiber helps to increase the payload capacity and endurance of drones, it allows a single flight mission to complete more workload, thereby improving operational efficiency and indirectly increasing economic benefits.
Maintainability
Simplify structural design: By utilizing the machinability of glass fiber, a simpler and more efficient drone structure can be designed, which is not only convenient for production and manufacturing, but also makes subsequent maintenance work simpler and faster.
Reduce the number of parts: Due to the high strength characteristics of glass fiber composite materials, sometimes one composite part can replace the functions of multiple traditional metal parts, which reduces the total number of parts required for assembly and reduces the risk of assembly errors.
Improve the convenience of fault detection: The glass fiber material itself has a certain degree of transparency, which means that in some cases, the status of internal components can be observed by naked eyes, which facilitates the timely detection and treatment of potential problems.
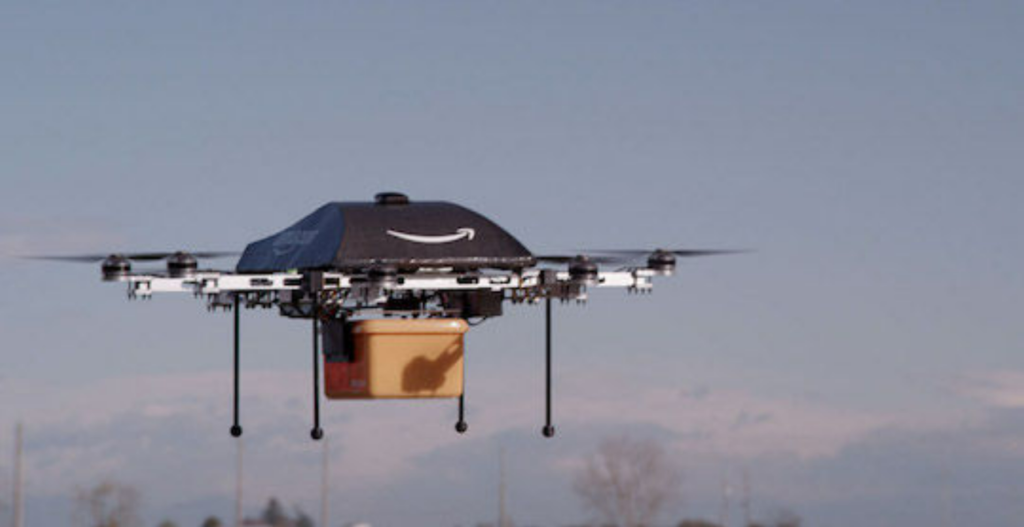
In Conclusion
Fiberglass significantly increases the load capacity of drones due to its lightweight characteristics. By reducing the weight of the fuselage, the drone can carry more payload, thus expanding its range of applications. Secondly, the use of fiberglass helps extend the battery life of the drone. Due to the reduction in weight, the drone consumes less energy during flight, allowing for longer flights. In addition, the economy of glass fiber also allows the manufacturing cost of drones to be effectively controlled and reduces subsequent maintenance costs. Finally, the workability and durability of fiberglass simplify the design and maintenance process of drones and improve overall operational efficiency.
As a leading company focusing on the research and development and production of high-quality glass fiber products, Aiswix has always been committed to promoting the innovative development of the drone industry. The glass fiber products provided by Aiswix not only meet the basic requirements of drone manufacturing for lightweight and high-strength materials, but also set an industry benchmark in terms of technological innovation and product quality. With its strong R&D capabilities and rich practical experience, Aiswix has continuously introduced new material solutions that meet market demand, bringing unprecedented changes to the drone manufacturing industry.