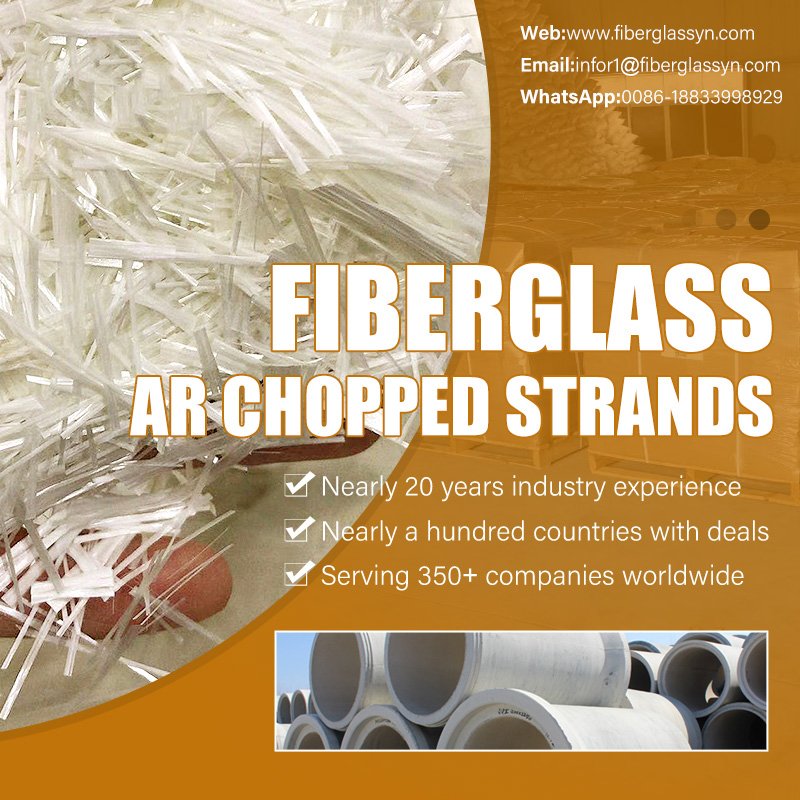
Introduce
The journey of chopped strand fiberglass begins with a blend of raw materials transformed through sophisticated processes. From its production to its unique characteristics and diverse applications, this material stands at the forefront of innovation. Have you ever wondered how the strands of fiberglass are meticulously created, weighed, and tested for strength? Or why industries ranging from construction to industry invest heavily in this material, and how do you maintain it to ensure longevity? Let’s dive into the fascinating world of chopped strand fiberglass and uncover the answers to these compelling questions.
What is Fiberglass Chopped Strands?
Fiberglass chopped strands is a form of glass fiber reinforcement material where continuous glass filaments are chopped into shorter lengths. These short fibers, typically ranging from a few millimeters to several centimeters, are used to reinforce various materials, primarily plastics and resins, creating composite materials with enhanced properties.
Fiberglass chopped strands is widely appreciated for its versatility and effectiveness in reinforcing a range of products. The chopped fibers are often bundled together and can be processed into different forms, such as mats, which are used in various molding processes. These mats are known for their uniform distribution of strength and ease of handling, making them a popular choice in the manufacturing of complex shapes and large parts.
In essence, chopped strands is a crucial material in modern manufacturing, offering a balance of strength, flexibility, and ease of use. Its ability to be molded into various shapes and combined with different resins makes it an indispensable resource for creating high-performance, durable products.
How are Fiberglass Strands Made?
The production of fiberglass strands is a fascinating process that involves transforming raw materials into fine, durable fibers. The primary ingredient for making fiberglass is silica sand, which is combined with other raw materials such as limestone, soda ash, and various minerals to achieve the desired properties.
Melting
The first step in the production process is melting the raw materials. This mixture is fed into a furnace, where it is heated to extremely high temperatures, often exceeding 1,400 degrees Celsius (2,552 degrees Fahrenheit). At these temperatures, the materials melt and form a molten glass.
Forming Fibers
The molten glass is then passed through a device called a bushing, which contains numerous small holes or nozzles. As the molten glass flows through these holes, it is rapidly cooled and pulled into thin strands or filaments. These filaments are incredibly fine, often thinner than human hair, and can be continuous or chopped into shorter lengths.
Sizing
To enhance the properties of the fiberglass strands, a chemical coating known as sizing is applied. Sizing serves multiple purposes: it protects the glass fibers from damage during handling, improves their bonding with resins, and enhances the overall performance of the composite material.
Chopping
For chopped strand fiberglass, the continuous glass filaments are cut into shorter lengths, typically ranging from a few millimeters to several centimeters. The chopping process is precise and controlled to ensure uniform fiber length.
Collection and Packaging
The chopped fibers are then collected and packaged for further use. They can be bundled together to form mats, rovings, or other forms depending on the intended application.
This production process results in fiberglass strands that are lightweight yet incredibly strong and durable. The ability to control the properties of the glass fibers through the selection of raw materials and the application of sizing makes fiberglass a highly versatile and valuable material in various industries.
How Much Does Fiberglass Chopped Strand Weight?
The weight of fiberglass chopped strand can vary significantly depending on several factors, including the length of the fibers, the density of the material, and the specific form it takes (e.g., loose fibers, mats, or rovings). Understanding the weight of chopped strand fiberglass is crucial for manufacturers as it influences the handling, processing, and final properties of the composite material.
- Fiber Length: Longer fibers tend to have a higher weight due to increased mass.
- Fiber Diameter: Thicker fibers contribute to a higher overall weight.
- Packing Density: How tightly the fibers are packed can affect the weight measurement.
- Importance of Weight in Applications: The weight of chopped strand fiberglass plays a crucial role in determining the mechanical properties and performance of the final composite material. Heavier mats or higher bulk density fibers can provide increased strength and durability, but they may also be more challenging to handle and process. Manufacturers must carefully balance the weight and other properties to achieve the desired performance for specific applications.
How Strong is Chopped Strands?
Chopped strand fiberglass is renowned for its impressive strength-to-weight ratio, making it a preferred material for reinforcing composites across numerous industries. Its strength derives from the inherent properties of glass fibers combined with the ability to distribute stress uniformly throughout the composite material.
One of the primary measures of strength for fiberglass is its tensile strength, which is the maximum stress it can withstand while being stretched or pulled before breaking. Chopped strand fiberglass typically exhibits a high tensile strength, often in the range of 1,700 to 3,000 MPa (megapascals). This makes it exceptionally strong for its weight, outclassing many metals and plastics in terms of specific strength (strength per unit weight).
Chopped strand fiberglass also offers excellent impact resistance, meaning it can absorb and dissipate energy from sudden impacts without fracturing. This property is particularly valuable in applications where the material must endure dynamic loads, such as in automotive components and sports equipment.
Flexural strength refers to the ability of a material to resist deformation under load. Chopped strand fiberglass composites often have high flexural strength, ensuring they maintain structural integrity under bending stresses. This is crucial in applications like boat hulls and construction panels, where the material must support loads without bending excessively.
The compression strength of chopped strand fiberglass is another important attribute, indicating how well the material can withstand compressive forces. While not as high as its tensile strength, the compression strength of fiberglass is still significant, contributing to its overall durability and versatility.
The strength of chopped strand fiberglass composites is not solely dependent on the fibers themselves. The type of resin used to bond the fibers and the manufacturing process also play critical roles. For instance, epoxy resins generally provide stronger bonds and higher performance than polyester resins. Additionally, the way the composite is fabricated, whether through hand lay-up, spray-up, or other methods, affects the final strength and quality.
In conclusion, the strength of fiberglass strands is a result of its high tensile, impact, flexural, and compression strengths. These properties, combined with its lightweight nature and versatility, make it a superior material for a wide range of applications where durability and performance are paramount.
What is fiberglass chopped strands used for?
Fiberglass chopped strands find versatile applications across a spectrum of industries, contributing significantly to enhancing the strength, durability, and performance of various composite materials. Here’s a detailed exploration of their applications in different fields:
Concrete Reinforcement
Fiberglass chopped strands are widely used in concrete to improve its tensile strength, impact resistance, and durability. They help prevent cracking and enhance the overall structural integrity of concrete structures such as bridges, tunnels, and buildings.
Cement Products
Fiberglass chopped strands are used in various cement-based products such as pipes, precast elements, and paving stones. They improve the flexural and tensile strength of cement, making it suitable for demanding construction applications.
Gypsum Board
Fiberglass chopped strands are incorporated into gypsum board manufacturing to enhance its strength, reduce cracking, and improve impact resistance. This ensures that gypsum board panels maintain their structural integrity and longevity.
Masterbatch
In the plastics industry, fiberglass chopped strands are mixed into masterbatches to reinforce thermoplastic materials. This reinforcement improves the mechanical properties of plastic products, including stiffness, dimensional stability, and heat resistance.
Brake Pads
Fiberglass chopped strands are added to brake pad formulations to enhance their thermal stability, friction properties, and wear resistance. This improves the performance and longevity of brake pads used in automotive and industrial applications.
Needle Felt
In textile manufacturing, fiberglass chopped strands are incorporated into needle felt materials used for filtration, insulation, and industrial applications. They add strength, durability, and dimensional stability to the needle felt products.
In summary, fiberglass chopped strands play a crucial role in enhancing the properties of composite materials across a wide range of applications. Their versatility, durability, and ability to reinforce various substrates make them indispensable in industries where strength, performance, and longevity are paramount. As technology advances and new applications emerge, fiberglass chopped strands continue to innovate and expand their impact on modern manufacturing and construction practices.
How Do You Clean Fiberglass Strands?
Maintaining and cleaning fiberglass strands is crucial for ensuring their longevity and performance in various applications. Proper cleaning techniques help remove contaminants, protect the fibers, and prevent damage. Here, we explore the best practices for cleaning fiberglass strands effectively.
Safety Precautions
When handling and cleaning fiberglass strands, it is essential to wear appropriate protective gear. Fiberglass can cause skin irritation and respiratory issues if not handled properly. Wear gloves, long sleeves, safety glasses, and a mask or respirator to protect yourself from fiberglass dust and particles.
Work in a well-ventilated area to minimize exposure to airborne fiberglass particles.
Dry Cleaning
For light dust and debris, a dry cleaning method can be effective. Use a soft brush or a vacuum cleaner with a brush attachment to gently remove dust and loose particles from the fiberglass strands. Be careful not to damage or break the fibers during this process.
Compressed air can also be used to blow away dust and debris. Ensure the air pressure is not too high to avoid damaging the fibers.
Wet Cleaning
For more thorough cleaning, a wet cleaning method is recommended. Prepare a mild detergent solution by mixing a gentle dish soap or a specialized fiberglass cleaner with warm water.
Dampen a soft cloth or sponge with the cleaning solution and gently wipe the fiberglass strands. Avoid scrubbing too hard, as this can damage the fibers or the sizing agent that protects them.
Rinse the fiberglass strands with clean water to remove any soap residue. Use a clean, damp cloth or a gentle spray of water to ensure all detergent is washed away.
Removing Stubborn Stains
For stubborn stains or sticky residues, use a mild solvent such as isopropyl alcohol or acetone. Apply the solvent to a soft cloth and gently rub the affected area. Be cautious with solvents, as they can degrade the sizing agent and weaken the fiberglass if used excessively.
After using a solvent, rinse the fiberglass strands thoroughly with clean water to remove any remaining solvent.
Drying
After cleaning, allow the fiberglass strands to air dry completely. Avoid using high heat or direct sunlight, as excessive heat can weaken the fibers and cause them to become brittle.
If time is a factor, use a fan to accelerate the drying process while ensuring gentle airflow.
Maintenance Tips
Regularly inspect glass fiber chopped strands for signs of contamination, damage, or wear. Prompt cleaning and maintenance can prevent more severe issues and extend the lifespan of the fiberglass.
Store fiberglass strands in a clean, dry environment to minimize exposure to dust, moisture, and other contaminants.
Handle fiberglass with care to prevent damage to the fibers. Avoid bending, crushing, or placing heavy objects on top of the strands.
Special Considerations for Composite Parts
When cleaning composite parts reinforced with fiberglass, such as boat hulls or car panels, follow the manufacturer’s guidelines for cleaning and maintenance. These parts may have additional coatings or finishes that require specific care.
For large composite structures, pressure washing with a gentle setting can be an effective cleaning method. Ensure the pressure is not too high to avoid damaging the surface.
In Conclusion
In conclusion, the exploration of fiberglass chopped strands reveals a material that is both innovative and indispensable in modern manufacturing. From its intricate production process to its remarkable strength and versatility, chopped strand fiberglass plays a pivotal role in various industries. Understanding the nuances of its weight, strength, and maintenance further underscores its importance. As technology and manufacturing techniques continue to evolve, the applications and potential of chopped strand fiberglass are bound to expand, solidifying its place as a cornerstone of material science.