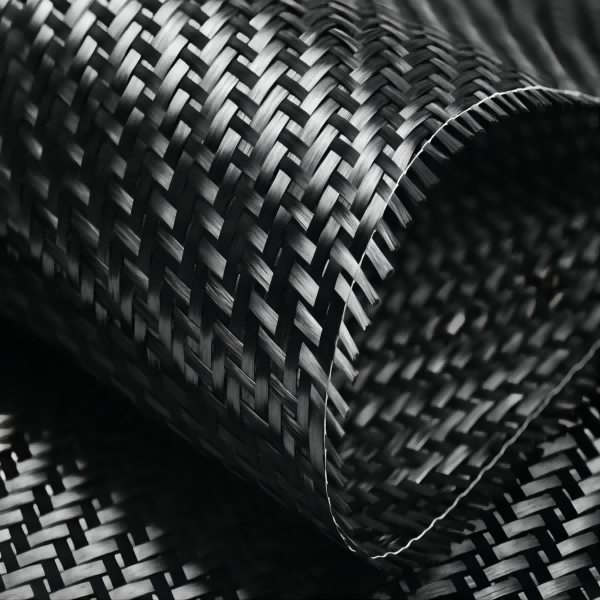
Introduce
With the continuous advancement of science and technology and the development of industry, composite materials, as a lightweight, high-strength, corrosion-resistant material, have been widely used in various fields. As an important component of composite materials, prepreg plays an increasingly important role in modern industry. This article aims to explore the application and market trends of prepregs and provide readers with comprehensive information and analysis for an in-depth understanding of this field.
Basic concepts and classification of prepregs
Prepreg, that is, pre-impregnated reinforcement materials, is a composite intermediate product made by impregnating a resin matrix with reinforcement materials under strictly controlled conditions. It is characterized by the uniform distribution of the resin matrix and reinforcement materials and the need for curing under high temperature and pressure during the preparation process. In the composite manufacturing process, prepregs not only need to have certain processability during preparation, but also need to have excellent performance in the end-use environment.
Characteristics of prepreg
- Uniform distribution: The resin matrix and reinforcement materials in the prepreg can be evenly distributed throughout the material, ensuring uniform performance of the composite material.
- High-temperature and high-pressure curing: During the preparation process, the prepreg needs to be cured under high temperature and high pressure to ensure sufficient bonding between the resin matrix and the reinforcing material, thereby improving the strength and durability of the material.
- Processability: Prepreg has a certain degree of processability during the preparation process, which facilitates subsequent processing and molding, and is suitable for manufacturing needs of various complex shapes.
- Partial curing: In order to facilitate post-processing, the resin matrix in the prepreg is usually only partially cured and stored in a cool place to prevent complete polymerization. During the manufacture of composite materials, it needs to be heated in an autoclave or oven to achieve complete polymerization.
Classification of prepregs
- Classification according to the physical shape of the reinforcement
Unidirectional prepreg: Reinforcement material with fibers aligned in the same direction, suitable for structural components that can withstand unidirectional forces, such as wind turbine blades.
Fabric prepreg: Reinforcement material in the form of fabrics with fibers interwoven in specific ways, suitable for manufacturing complex structures that can withstand multi-directional forces, such as car bodies.
2.Classification according to the physical shape of the reinforcement
Broadband prepreg: suitable for the manufacturing of large-area structural components, such as wings, fuselages, etc. in the aerospace field.
Narrow prepreg: often used to make small parts or as reinforcement materials, such as reinforcements for sports equipment.
3.Classification by type of reinforcement
Carbon fiber reinforced prepreg: It has the characteristics of high strength and light weight, and is suitable for aerospace, advanced sports equipment and other fields.
Glass fiber reinforced prepreg: lower cost, widely applicable, such as automobile, construction and other industries.
Aramid fiber reinforced prepreg: has excellent tensile strength and impact resistance, and is often used in safety protection fields such as bulletproof equipment.
Prepreg preparation technology
The preparation technology of prepreg is one of the key factors affecting its performance and application range. Below we will describe the common prepreg preparation process and the impact of the preparation process on prepreg performance.
Common prepreg preparation processes
- Impregnation method: Impregnation method is one of the most common prepreg preparation processes. In this process, fibers are usually placed in resin and impregnated for a period of time to allow the resin to fully penetrate into the fiber. The resin is then cured by drying or other means to form a prepreg. This process is simple and easy to implement and suitable for various types of prepregs.
- Spray coating method: Spray coating method is a preparation process for coating resin on the surface of reinforced materials. The resin is usually sprayed evenly on the fiber surface using a spray gun or spray equipment, and then the resin is cured by thermal curing or chemical curing to form a prepreg. This process is suitable for preparing prepregs with larger areas and larger demand.
- Impregnation-calendering method: The impregnation-calendering method combines the impregnation and calendering processes. The fibers are first impregnated in resin, and then the impregnated fibers are laminated into sheets through calendering equipment. Finally, the prepreg is formed by thermal curing or other curing methods. The prepreg prepared by this process has better compaction and consistency.
- Pre-preg method: Pre-preg method is to pre-bond the impregnated fiber layer and resin film together, and then solidify the resin under appropriate conditions to form a prepreg. This process is suitable for situations where reinforcement materials and resins need to be pre-combined, which can improve production efficiency.
Effect of preparation process on prepreg properties
The preparation process of prepreg directly affects its performance and application scope. The following are the main influencing factors of the preparation process on prepreg performance:
- Resin impregnation degree: The preparation process directly affects the penetration and distribution uniformity of resin in the fiber, which in turn affects the performance of the prepreg. If the resin is not impregnated enough, the bond between the fiber and the resin may not be strong; if it is over-impregnated, the density and cost of the prepreg may be increased.
- Curing conditions: Different curing conditions (such as temperature, pressure, curing time, etc.) will directly affect the curing degree and performance of the prepreg. Precision in controlling the curing conditions is critical to prepreg quality.
- Fiber direction and arrangement: The direction and arrangement of fibers during the preparation process will affect the mechanical properties and directional properties of the prepreg. Therefore, precise control of fiber direction and arrangement is required during the preparation process.
- Resin type and proportion: Different types and proportions of resin will affect the heat resistance, corrosion resistance and mechanical properties of prepregs. Choosing the right resin type and ratio is key to making high-performance prepregs.
In summary, the preparation process of prepreg has an important impact on its performance. Therefore, various preparation parameters need to be accurately controlled during the production process to ensure that the quality and performance of prepreg meet the requirements.
Applications of prepregs in various fields
As a key composite intermediate product, prepreg is widely used in various fields. Below we will describe application cases in aerospace, automobile manufacturing, energy industry, sports and leisure products, and other fields.
In the aerospace industry, lightweight and high strength are crucial requirements. Prepreg has become the first choice for aerospace materials due to its excellent performance. For example, carbon fiber composite materials made of prepreg are widely used in aircraft fuselages, wings, spacecraft structures and other components, which can significantly reduce the weight of aircraft and improve their fuel efficiency and performance.
In the automotive manufacturing industry, prepregs also play an important role. Carbon fiber prepreg and glass fiber prepreg are widely used in the manufacturing of automotive body, chassis, interior and other components. They can improve the structural strength and safety of the vehicle, while reducing the overall weight of the vehicle and improving fuel economy.
In the energy industry, prepregs are also increasingly used. For example, composite materials made of prepreg are widely used in the wind and solar fields to manufacture key components such as wind power blades and solar photovoltaic brackets. They have excellent durability and weather resistance and can improve the efficiency and reliability of energy equipment.
In the field of sports and leisure products, prepregs also play an important role. For example, carbon fiber composite materials made of prepregs are widely used to manufacture high-performance sports equipment such as golf clubs, tennis rackets, and bicycle frames. They are lightweight, strong, and have excellent performance, which can improve the competitive level of athletes.
In addition to the fields mentioned above, prepregs are also used in some other fields. For example, in the construction field, composite materials made of prepreg are used to manufacture high-strength and corrosion-resistant building materials, such as exterior wall panels, roof structures, etc. In the electronics industry, prepregs are also used to manufacture components such as housings and brackets for electronic equipment, with good antistatic properties and durability.
Prepreg is widely used in various fields. Its excellent performance and diverse preparation processes make it one of the indispensable key materials in modern industry. With the continuous advancement of technology and the expansion of application fields, the application prospects of prepregs will be broader.
In Conclusion
As a key composite intermediate product, prepreg will usher in broader prospects in future development. With the acceleration of global industrialization and the growing demand for high-performance materials, prepreg, as a lightweight, high-strength, corrosion-resistant material, will be more widely used. In the future, with the continuous innovation of technology and the continuous improvement of preparation processes, the performance and quality of prepregs will continue to improve, allowing them to play a more important role in various fields.
At the same time, with the increasing global awareness of environmental protection, the requirements for sustainable development are also getting higher and higher. As an environmentally friendly and renewable material, prepreg will receive more attention and attention in the future. In the future, Aiswix‘s prepreg preparation process will be more environmentally friendly and energy-saving, and it will also pay more attention to the recyclability of materials to meet society’s needs for environmental protection and sustainable development.