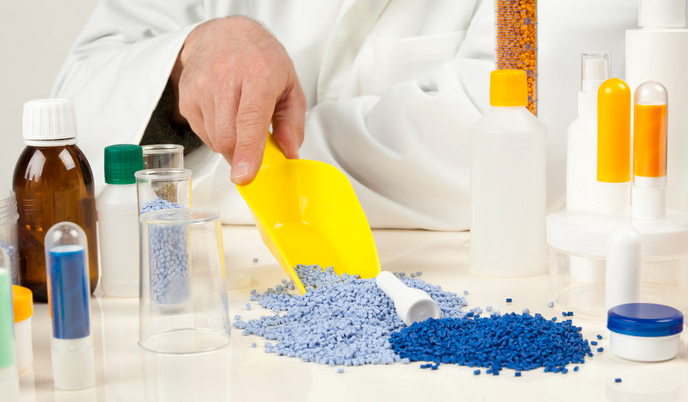
Introduce
This paper reviews the latest research results of fiber-reinforced nylon composites and their applications in different industrial fields. First, the basic concepts and technological progress of nylon composites are introduced, and then the performance characteristics of high-performance fiber (such as glass fiber and carbon fiber) reinforced nylon composites and their applications in automobiles, aerospace, 3D printing and other fields are analyzed. Finally, future development trends and technical challenges are discussed.
As an important engineering plastic, polyamide (nylon) occupies an important position in many fields due to its excellent mechanical properties, heat resistance, wear resistance and good processing performance. In recent years, with the development of high-performance fiber reinforcement technology, fiber-reinforced nylon composites have been increasingly used in the automotive, aerospace and other industries due to their higher strength, stiffness and dimensional stability. This paper aims to review the technological innovation and industrial application progress of fiber-reinforced nylon composites.
Basics of Nylon Composites
Classification and Properties of Polyamides
Polyamides (nylons) are a class of linear or branched polymers synthesized by the polycondensation reaction of diamines and dibasic acids. Common types of nylons include nylon 6, nylon 66, and nylon 610, each of which has unique performance characteristics. For example, nylon 66 is known for its high melting point and excellent mechanical properties.
- Nylon 6: This is one of the most common types of nylons and is favored for its excellent strength, wear resistance, and good processing properties. Nylon 6 is widely used in textiles, carpets, ropes, and industrial belts.
- Nylon 66: Nylon 66 is known for its higher melting point and better mechanical properties and is often used to produce high-performance engineering plastics and fibers. It has a wide range of applications in the automotive, aviation, and electronics industries.
- Nylon 610: Nylon 610 combines the characteristics of nylon 6 and nylon 11, has good mechanical properties and chemical resistance, and is suitable for the production of high-performance engineering plastics and fibers. Generally, fiber reinforcement can improve the mechanical strength of nylon to reach the strength of metal materials and replace metal. For example, compared with nylon 66 materials, glass fiber reinforced nylon 66 composite materials have higher rigidity and modulus, good dimensional stability, high impact strength, and low cost. They can be widely used in automobile engine intake pipes, intercooler pipes, covers, and automobile steering system sensor covers, chassis system housings and other related parts.
Principle of fiber reinforcement technology
Fiber reinforcement refers to the process of adding various types of fibers (such as glass fibers, carbon fibers, etc.) to the nylon matrix to improve its mechanical properties. Fibers can significantly improve the tensile strength, stiffness and heat resistance of composite materials while maintaining a low density.
Comparison of common fiber types and their properties
Fiberglass: low cost, good insulation and chemical resistance.
Carbon fiber: low density, high strength, good conductivity, but higher cost.
Technological innovation
High-performance fiber-reinforced nylon composites
- Carbon fiber reinforced nylon composites
Performance characteristics: Carbon fiber reinforced nylon composites have extremely high strength-to-weight ratio and rigidity, and also show good corrosion resistance and dimensional stability.
Preparation method and process improvement: Carbon fiber is mixed with nylon matrix by melt blending or solution blending, and processed by screw extruder to form a uniformly distributed composite material. In addition, the comprehensive performance of the material can be further improved by optimizing the length and content of carbon fiber.
- Fiberglass reinforced nylon composites
Performance characteristics: Glass fiber reinforced nylon composites have good strength, stiffness and heat resistance, and the cost is relatively low.
Preparation method and process improvement: By controlling the length, content and surface treatment of the fiber, the mechanical properties and processing properties of the composite material can be effectively improved.
Functionalization and surface modification
- Fiber surface treatment technology: Change the surface properties of the fiber by chemical or physical methods to enhance the interfacial bonding between the fiber and the nylon matrix, thereby improving the overall performance of the composite material.
- Progress in functionalization of composite materials: By introducing functional additives (such as conductive particles, nanoparticles, etc.), composite materials can have specific functional properties, such as electromagnetic shielding, conductivity, etc.
- The impact of surface modification on the performance of composite materials: Surface modification can not only improve the compatibility between fiber and matrix, but also give composite materials additional performance advantages.
Application of 3D printing technology
- Development of printing technology and equipment: With the advancement of 3D printing technology, continuous fiber-reinforced nylon composite materials can be printed by FDM/FFF (fused deposition modeling) and other methods.
- Printing parameter optimization and performance regulation: By adjusting parameters such as printing speed, temperature, fiber arrangement direction, etc., the microstructure of the composite material can be precisely controlled, and then its mechanical properties can be regulated.
- Post-processing technology and its role: Post-processing steps such as annealing can further improve the crystallinity and mechanical properties of the composite material.
Industrial Applications
- Application Cases: Glass fiber reinforced nylon 66 composites are widely used in automotive intake manifolds, engine hoods, side doors, rearview mirror connectors, fan blades and other parts.
- Lightweight design and energy saving and emission reduction: The use of fiber reinforced nylon composites can reduce the weight of the car, help improve fuel efficiency and reduce emissions.
- Cost-benefit analysis: Although the initial investment may be high, in the long run, the use of fiber reinforced nylon composites can reduce overall costs and improve the performance and durability of the car.
- High performance requirements and special environmental adaptability: Aerospace applications have extremely strict requirements on materials, including lightweight, high strength, high temperature resistance, corrosion resistance, etc.
- Application Cases and Technical Challenges: Carbon fiber reinforced nylon composites are widely used in aircraft structural parts and components, such as wing beams, fuselage components, etc.
- Balance between lightweight and safety: Achieving structural lightweight while ensuring safety is an important goal in the aerospace field.
- Customized component design and manufacturing: 3D printing technology makes it possible to produce components with complex shapes, which is particularly important for meeting personalized needs.
- Rapid prototyping and small batch production: 3D printing technology shortens the product development cycle and reduces the cost of small batch production.
- Personalized medical equipment and sports goods: The application of fiber-reinforced nylon composites in customized medical equipment and high-performance sports goods is expanding.
Development Trends and Prospects
Future research will focus on the development of new high-performance fibers and how to better combine these fibers with other high-performance materials to create more advanced composite systems.
With the development of the Internet of Things and smart sensing technology, future fiber-reinforced nylon composite materials will integrate more intelligent functions.
Environmental protection and sustainability will be the key directions for the development of materials science in the future, so the development of recyclable and biodegradable fiber-reinforced nylon composite materials will become an important topic.
In Conclusion
Fiber-reinforced nylon composites have become one of the hot topics in materials science research due to their excellent performance and wide industrial application prospects. With the continuous advancement of technological innovation, these materials will further improve the competitiveness of industries such as automobiles and aerospace, and also provide new possibilities for 3D printing technology. In the future, with the development of new fiber materials and the enhancement of environmental awareness, the application of fiber-reinforced nylon composites will be more extensive.