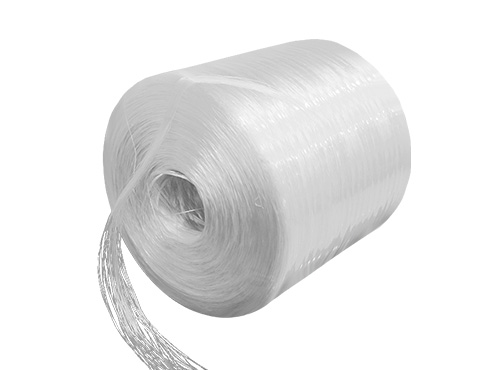
Introduce
Have you ever wondered about the fascinating world of fiberglass roving? What secrets lie within those rolls of continuous fiberglass strands? How is this versatile material manufactured, and what are its various types and applications? Join us on a journey of discovery as we delve into the intricate details of glass fiber roving, exploring its origins, manufacturing processes, and the myriad ways it is utilized across industries.
What is Fiberglass Roving?
Fiberglass roving consists of glass fibers bound together in a continuous strand, resembling a roll of fine threads. What sets fiberglass roving apart is its ability to be adapted to various shapes and forms, making it an indispensable component in numerous industries.
Fiberglass roving roll essentially acts as the backbone for reinforced plastics and composites. Its composition typically involves E-type glass, renowned for its exceptional strength and resistance to chemicals. This glass is meticulously melted and drawn into fine filaments, which are then assembled into strands to form the fiberglass roving roll. The result is a material that possesses outstanding mechanical properties, making it ideal for applications where strength, durability, and flexibility are paramount.
How is Glass Fiber Roving Made?
Glass fiber roving is the result of a meticulous manufacturing process that begins with the transformation of molten glass into fine filaments. The first step involves heating raw materials like silica sand, limestone, and soda ash to create molten glass. This molten glass is then drawn through tiny openings, creating the delicate fibers that form the basis of fiberglass roving gun.
The drawn-out fibers are subsequently gathered and assembled into continuous strands. The assembly process involves carefully aligning the fibers to ensure uniformity and strength throughout the roving. The final product, assembled fiberglass roving, embodies the robustness and versatility of glass fibers, ready to be employed in a myriad of applications.
Fiberglass roving essentially acts as the backbone for reinforced plastics and composites. Its composition typically involves E-type glass, renowned for its exceptional strength and resistance to chemicals. This glass is meticulously melted and drawn into fine filaments, which are then assembled into strands to form the fiberglass roving roll. The result is a material that possesses outstanding mechanical properties, making it ideal for applications where strength, durability, and flexibility are paramount.
Different Types of Fiberglass Roving
Fiberglass roving comes in various types, each tailored to meet specific industry requirements. One prominent variant is E glass roving, where the “E” stands for electrical. E glass roving is specifically designed to exhibit excellent electrical insulation properties, making it a preferred choice in industries where electrical components require reinforcement.
Another noteworthy type is fiberglass gun roving, a specialized form designed for applications involving spray guns for resin application. This type of roving ensures an even and controlled distribution of resin, making it ideal for applications like boat manufacturing and other intricate composite structures.
Understanding the different types of continuous fiberglass roving is crucial for selecting the right material based on the specific demands of a project. Whether it’s enhancing structural integrity, ensuring electrical insulation, or facilitating efficient resin application, the diverse types of fiberglass roving cater to a wide spectrum of needs.
Why Different Types of Fiberglass Roving?
The diversity in types of fiberglass roving stems from the varied demands of industries and applications. Different projects require different attributes from the reinforcement material, and manufacturers respond by developing specialized types of fiberglass roving.
For instance, the electrical and chemical resistance of E glass roving makes it indispensable in the production of electrical components. On the other hand, fiberglass gun roving‘s design suits applications where precise resin application is essential. By tailoring the characteristics of fiberglass roving, manufacturers ensure that it meets the specific needs of each industry, ultimately leading to more efficient and reliable end products.
Using Fiberglass Roving for Felting
The world of craftsmanship and artistry has found an unexpected ally in fiberglass roving. Can you use fiberglass roving for felting? The surprising answer is yes. While traditionally associated with industrial applications, fiberglass roving manufacturer has ventured into the realms of artistic expression. Craftsmen and artists have discovered that the unique properties of fiberglass roving can add strength and structure to felted creations.
When incorporated into felting projects, fiberglass roving brings an added dimension of durability and resilience. It becomes a supporting structure within the felted material, allowing artists to create intricate and robust sculptures. This unanticipated application showcases the adaptability of roving glass fiber, demonstrating its ability to transcend its conventional uses and inspire creativity in unexpected ways.
How to Use Fiberglass Roving
The versatility of glass fiber roving price extends far beyond its traditional roles in industrial and artistic applications. Understanding how to use fiberglass roving opens up a world of possibilities for engineers, craftsmen, and manufacturers alike.
In boat manufacturing, fiberglass roving reinforces hulls, providing the strength needed to withstand the harsh conditions of the sea. Automotive components benefit from the lightweight yet durable nature of glass fiber roving, contributing to fuel efficiency without compromising on strength. In the construction industry, fiberglass roving reinforces concrete, ensuring the longevity and structural integrity of buildings.
The process of using fiberglass roving roll involves incorporating it into the matrix or resin material. Whether it’s hand-laid in small-scale projects or used with advanced automated processes, fiberglass roving plays a pivotal role in creating robust and long-lasting composite structures. Its adaptability and ease of use make it a go-to choice for applications ranging from large-scale industrial projects to intricate and customized designs.
In Conclusion
Fiberglass roving stands as a testament to the marvels of material science. From its inception as molten glass to its diverse applications in construction, manufacturing, and even art, fiberglass roving gun continues to shape the way we approach innovation and creativity. As we unravel the secrets behind its manufacturing, understand its various types, and explore its unexpected uses, fiberglass roving emerges not just as a material but as a symbol of endless possibilities. So, are you ready to embrace the world of fiberglass roving and unlock its full potential? The journey promises to be as captivating as the material itself.